Policy
We will prioritize safety and accident prevention in all business activities. We will continue to operate without accidents or injuries, contributing to the safety of society, and strive to protect the safety and health of all individuals engaged in work at our business sites, including employees and subcontractors, and to create a comfortable working environment.
Safety Philosophy and Safety Policy
Safety Philosophy
We place the highest priority on safety and compliance in all our business activities.
Safety Policy
Safety comes first.
Recognizing that safety is the foundation of our Group business activities, and with a strong determination to ensure that no one will be injured or will injure others, we will work on the following as our basic policy.
Observance of basic safety rules
Execution of health and safety activities
Improvement of crisis management capabilities
System
The Sanyo Chemical Group has established an Environment and Safety Group at each factory for occupational safety and health, security, and disaster prevention at each of its production bases. The Environment and Safety Dept.’s Safety Promotion Group directs and supervises all production sites, including research laboratories, the Head Office, branch offices, and sales and marketing offices.
In case of an emergency, a local emergency task force is established in the region where the emergency has occurred. Should a large-scale earthquake or other wide-area disaster occur, the Business Continuity (BC) Task Force will be set up at the Head Office to implement support and reconstruction activities on a company-wide level under the control of the General Manager of the Environment and Safety Headquarters designated by the President.
System Diagram
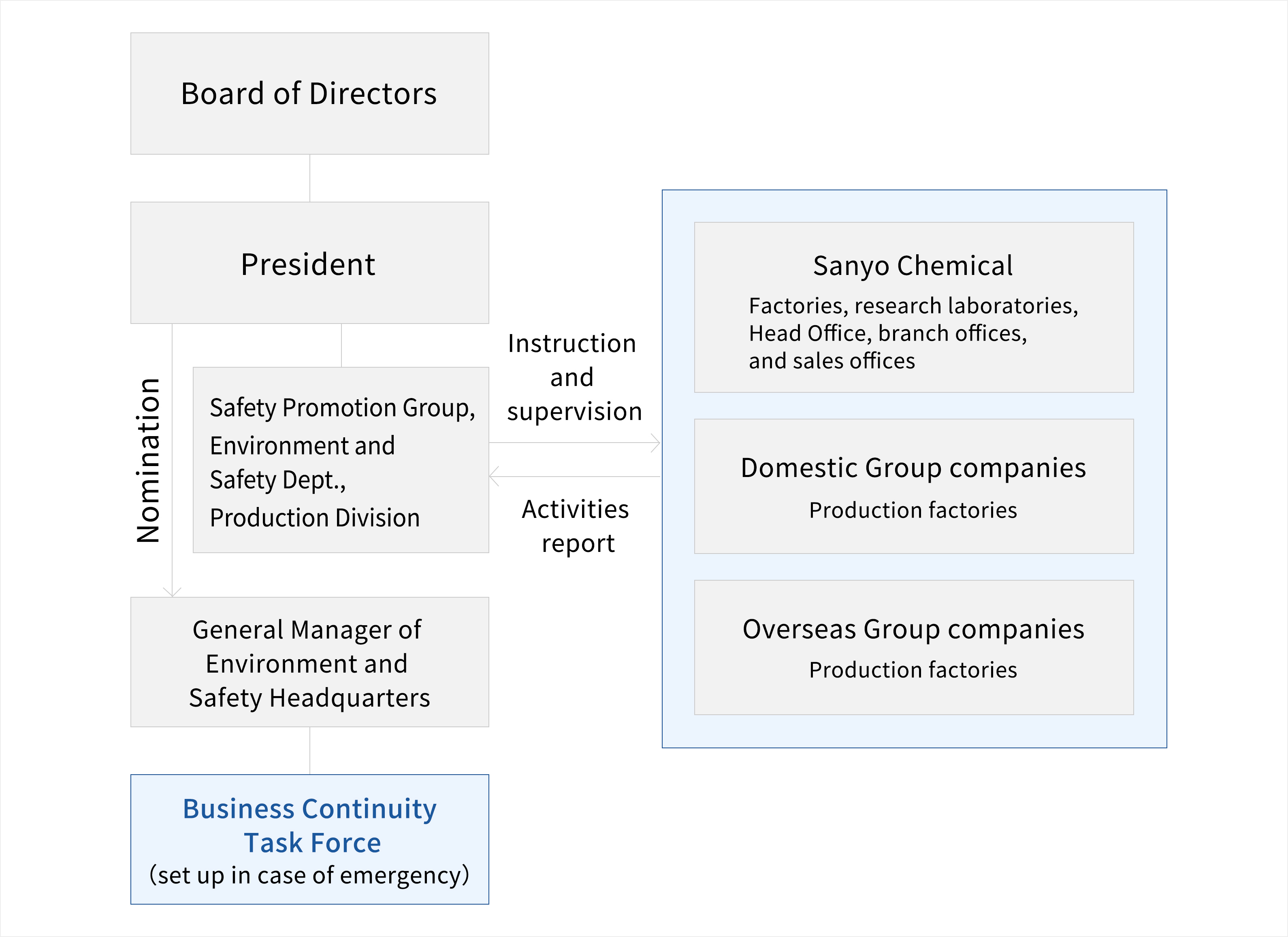
Safety Promotion Group, Environment and Safety Dept.
Led by the Safety Promotion Group of the Environment and Safety Dept., we conducted a safety assessment by the Japan Industrial Safety Competency Center at two sites, the Nagoya Factory and the Kashima Factory, for the purpose of objective safety evaluation by a third party. Based on the results of this assessment, we will make further efforts to improve process risk assessment and foster a safety culture. In these initiatives, we will involve external safety experts and incorporate a technical perspective to further enhance safety. In FY2024, we conduct process risk assessment training for managers in manufacturing sites.
Status of Labor Accidents
In order to achieve zero labor accidents, we are conducting activities under the main themes of risk assessment, creation of a workplace culture in which workers warn each other, thorough implementation of recurrence prevention measures, and achievement of a safer work environment.
In FY2023, in addition to one occupational accident involving our employees with lost time and ten without lost time, there were two occupational accidents involving dispatched workers/subcontractors with lost time and four without lost time.
We have investigated the actual causes of each accident by using the five whys method*1, implemented recurrence prevention measures, and rolled out important countermeasures to all Group factories in Japan and abroad.
- Five whys method: An analytical method to extract not only the direct cause but also the root cause behind a certain problem by repeating the process of identifying the cause why it occurred and asking the question “Why?” regarding that cause.
Occupational accident frequency rate*2
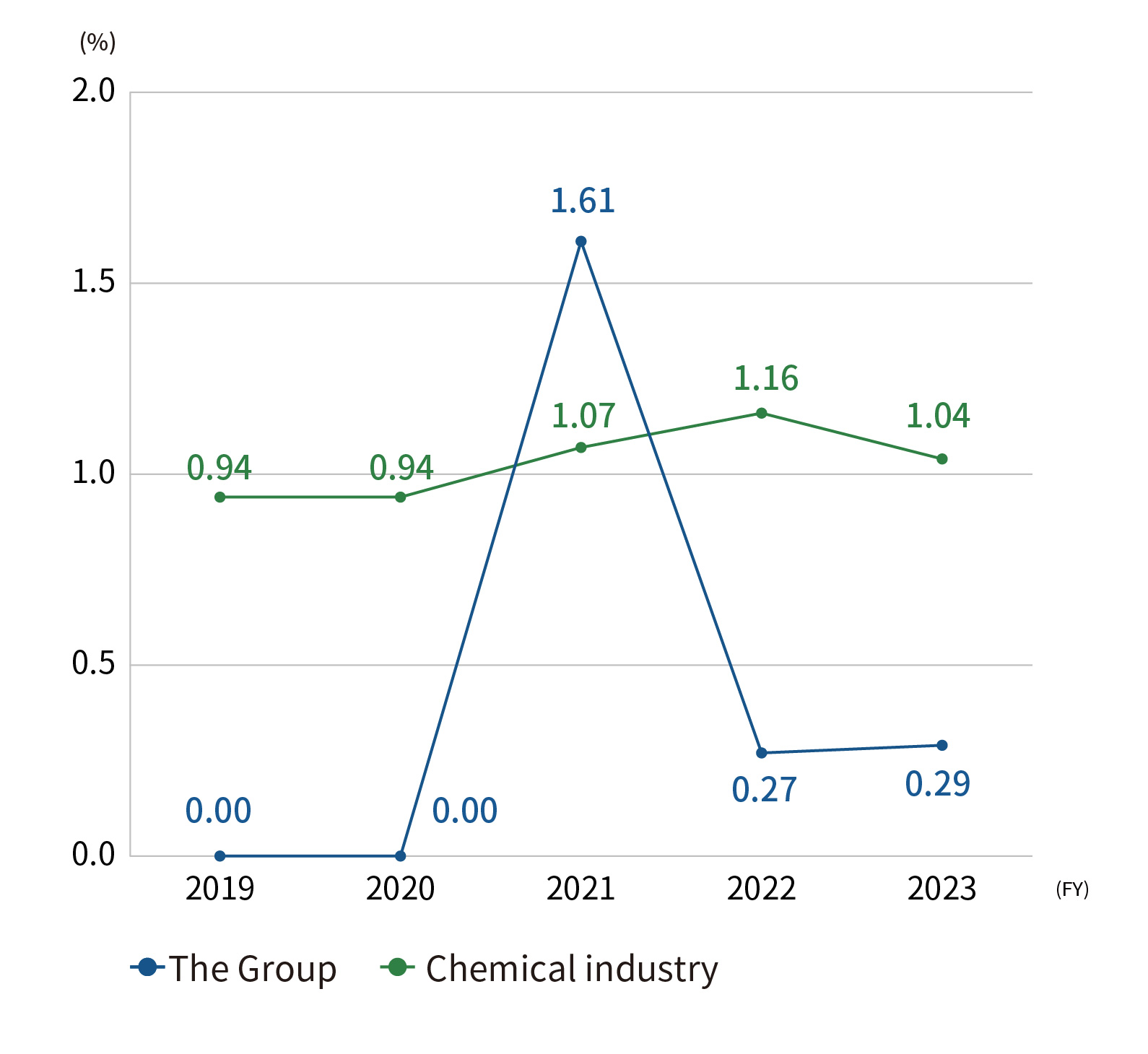
*2 Frequency rate = (number of employees suffering accident with lost time) ÷ (total working hours) × 1,000,000
This value indicates the generation frequency of accident victims per 1 million working hours.
Severity rate of occupational accidents *3
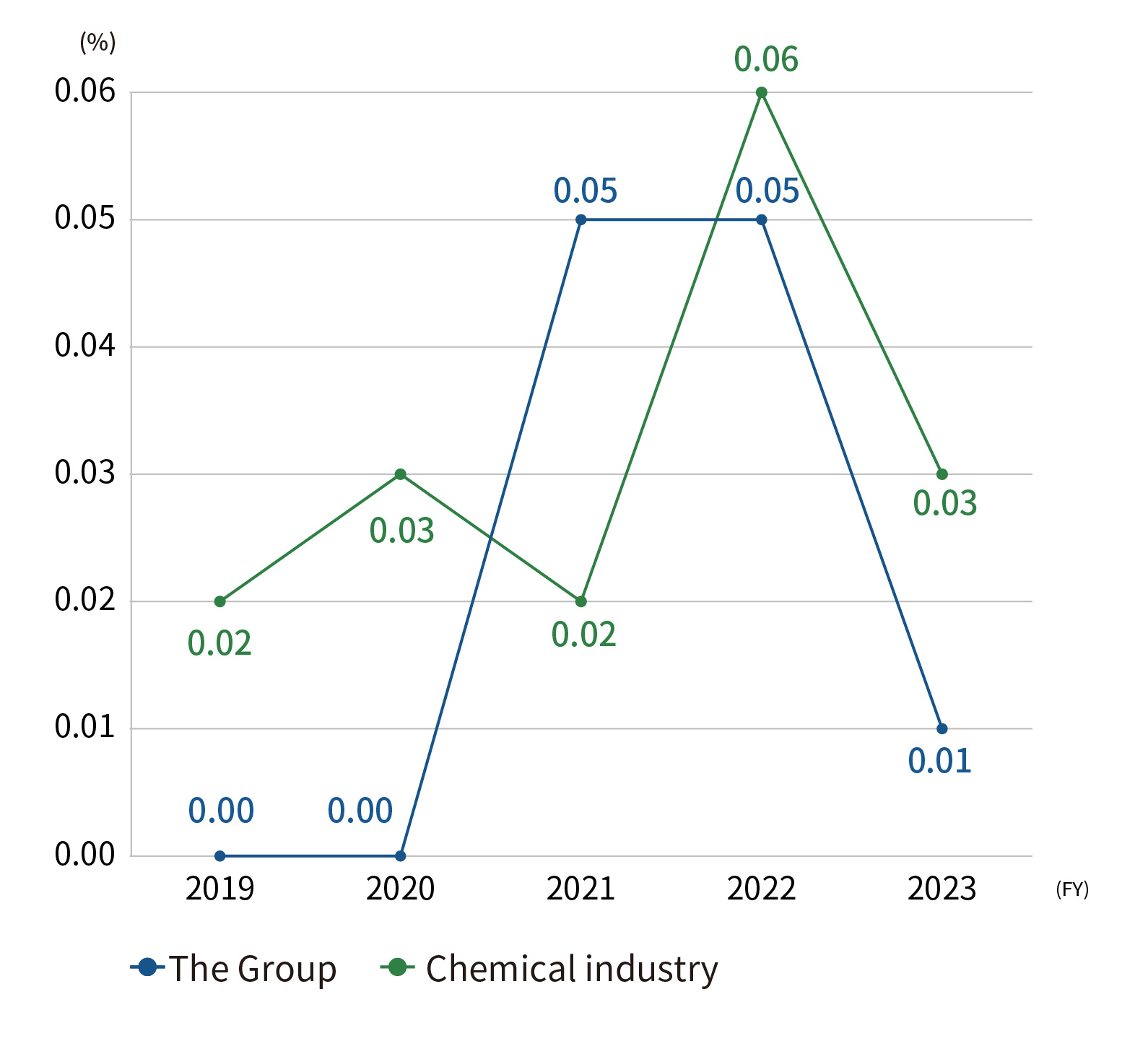
*3 Severity rate = (labor lost days) ÷ (total working hours) × 1,000
This value indicates the severity of accidents per 1,000 working hours.
Safety and Technology Education Center
In 2012, we opened the Safety and Technology Education Center at the Nagoya Factory with the aim of improving safety education and production technology. At this facility, participants can learn principles and theories by using devices that allow them to experience the danger of labor accidents and that simulate production site equipment. In addition, we are improving safety education by introducing videos of past accidents and virtual reality. A total of more than 3,400 employees and subcontractor employees have been trained to date.
Safety / Technology Education
(unit: people)
*Horizontally scrollable
FY2019 | FY2020 | FY2021 | FY2022 | FY2023 | ||
---|---|---|---|---|---|---|
Participants | Employees (including transfers) | 210 | 93 | 168 | 96 | 169 |
Subcontractor employees | 71 | 12 | 35 | 20 | 141 | |
Visitors and guests | 394 | 19 | 55 | 47 | 109 |
Risk assessment
The Group systematically conducts risk assessments of target chemical substances handled at its plants and research laboratories and takes necessary risk mitigation measures.
Although we have been working on physical measures and the establishment of rules, we will strengthen risk assessments to reduce risks.
The Safety Promotion Group is committed to the long-term development of personnel who can appropriately identify risks and devise mitigation measures, as well as introducing external wisdom and knowledge on safety to create mechanisms to enhance the safety capabilities of production sites.
Safety and Accident Prevention Activities
For safe operations and business continuity, we have implemented measures on both the hardware and software fronts, and have also established response and action plans in the event of any emergency situations, which we regularly practice through training.
Unusual situation handling training and emergency response
In accordance with the annual schedule, we repeatedly conduct training in cooperation with the local community, such as training for unusual situation handling in the unlikely event of an earthquake, fire, leakage, or other contingencies, and joint training with neighboring factories and local fire brigades.
In particular, in recent disaster prevention drills, we are conducting training without using scenarios to enhance practical response capabilities.
To prevent the past serious work-related accidents from being forgotten, the Company-wide Safety Day was established (held every October), where various events related to safety such as emergency training, evacuation training, emergency contact training, safety patrols, and safety talks are conducted in various regions both in Japan and overseas.
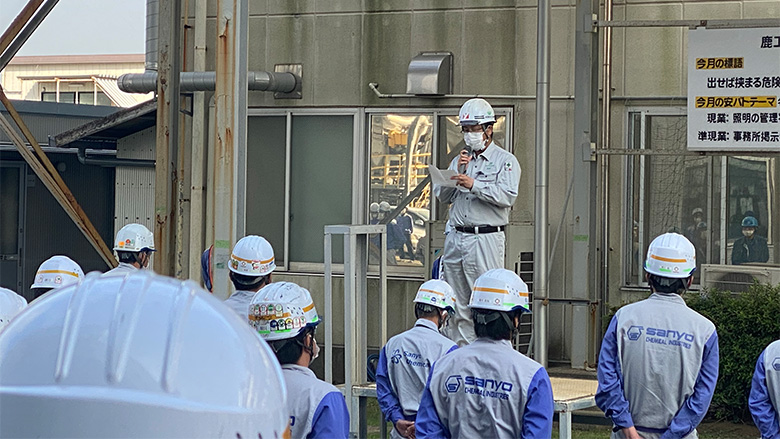
Kashima Factory: Safety talk by subcontractors
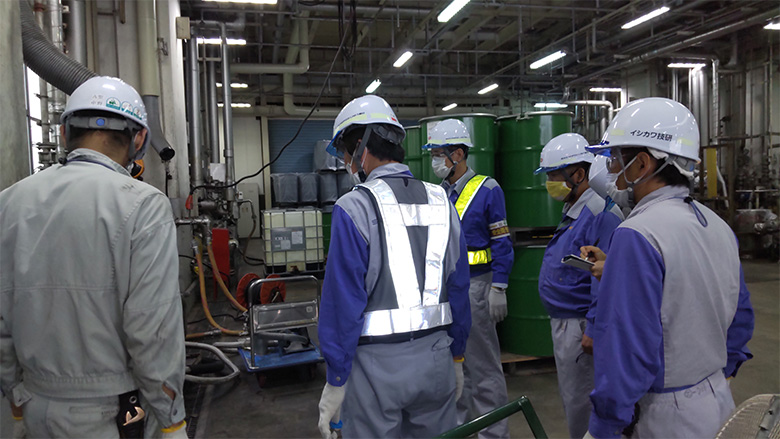
Nagoya Office in SAN NOPCO LIMITED: Safety patrols by managers
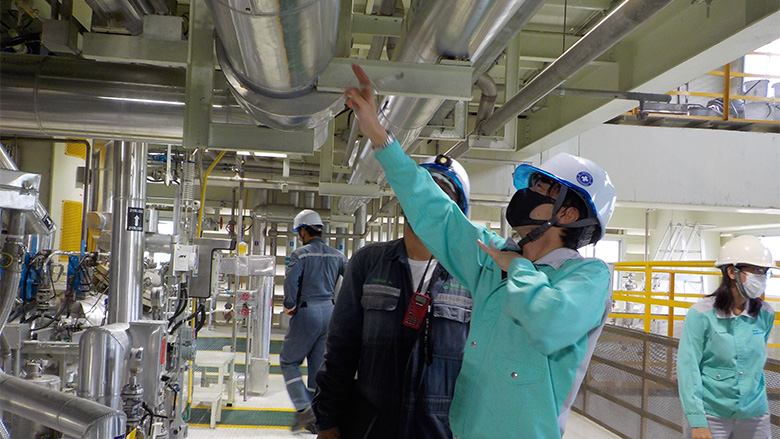
Sanyo Kasei (Thailand) Ltd.: Safety patrols
Earthquake preparedness
Following the Great Hanshin-Awaji Earthquake in 1995, we have continued to implement seismic reinforcement of buildings and production facilities. In addition, since 2007, we have been working on the formulation of a business continuity plan (BCP) and training. Kashima Factory was damaged in the 2011 Great East Japan Earthquake, but it was able to quickly resume operations as a result of BCP training. Based on this disaster experience, we are continuously conducting reviews of BCP training and response manuals.
Predictive maintenance and accident prevention measures
We have started predictive maintenance using artificial intelligence (AI) and digital transformation (DX) to measure and monitor the condition of equipment and replace or repair parts at the appropriate timing.
We believe that this approach can help reduce unnecessary part replacements and unexpected issues compared to the method of performing regular maintenance.
Furthermore, a system has been introduced where skilled workers can view and give instructions based on the footage from smart glasses worn by on-site workers from outside factories.
In addition, initiatives at each factory are shared through web communication tools and company-wide announcements at safety conferences to help strengthen accident prevention measures.
Internal Audit on Environment, Safety, and Disaster Prevention
The Responsible Care Dept. and the Safety Promotion Group of the Environment and Safety Dept. visit each factory once a year to conduct audits on environment, safety, and disaster prevention.
In the FY2023, we audited the horizontal deployment status of accident countermeasures, compliance with various regulations, implementation status of leakage prevention measures, and implementation status of risk assessments.
We are also conducting environmental management audits to replace the ISO14001 certification that was returned at our domestic factories.